|
Shock Wave Theory – Rifle Internal Ballistics, Longitudinal Shock Waves,
and Shot Dispersion
Introduction
I started looking at the causes of shot to shot
dispersion after getting serious for the first time with loading for
accuracy. I ran across Dan’s site (green788) and the concept of OCW. I was
intrigued by the undeniable fact that a single load recipe can work so well
across many different rifles, with different barrel lengths, diameters, and
bedding methods. I started reading everything I could get my hands on
regarding barrel vibration and the internal ballistics of a rifle during the
firing event. The singular thing that I could not get past was that a simple
harmonic vibration pattern could not explain the fact that a single load
could work with so many different rifles.
I am a radio communications electronics engineer by
profession, and deal with resonance and vibration all the time with antennas
and other circuits. It is physically impossible for all the different rifles
to have exactly the same harmonic pattern with relation to the bullet exit
time. Even a simple change in a barrel contour for a given length will
change the resonance, much less a change from a 24” tactical barrel to a 27”
target barrel. I am compulsive in the fact that I HAVE to have a clear model
and theory of why something works before being comfortable with it. I do bow
to expediency often, and just use a process or a machine without questioning
how it works, but for anything that I am trying to understand and improve
on, I have to have a good model.
Observations and the Resultant Questions
So, I started thinking about other possible reasons for
the dispersion of shots within a string. During literally thousands of very
careful load charge and seating depth experiments, some notable things were
observed:
- The point of impact (POI) moved slowly around as
the load was increased, the basic premise of Dan’s OCW method.
- The size of the group or the dispersion around
that POI varied VERY quickly as the seating depth was changed.
- The velocity deviation of a load would varied VERY
quickly as the seating depth was changed.
- Optimum loads work across multiple rifles, with
different length barrels.
Even 0.3 grains difference in a 25 grain .223 AI load
was enough to take it from a 0.5 MOA group to a 1.2 MOA group. Keep in mind
these were not single three shot groups, but typically 2 or more groups of 5
shots each at each load condition to validate the measurement. When I looked
a keeping the load constant and changing the seating depth, I saw the same
very quick changes in dispersion. As little as 0.010” sometimes affected the
groups by the same amount as previously described. The velocity deviation
changed rapidly as well. I often observed a reverse correlation between
velocity deviation and groups size during these experiments, where loads
producing good groups had a high standard deviation of velocity, and vice
versa. This was not always the case, in fact, once a truly OCW load was
achieved, it became quite tolerant to these changes with respect to
dispersion and velocity deviation, again validating Dan’s premise.
Here is what drove me nuts for weeks: A charge change
of 0.3 grains or a seating depth change of 0.010” changes the velocity very,
very little, usually less than 50 FPS at a mean velocity of around 2900 FPS.
The change to the groups, on the other hand, was dramatic.
Why? ? ?
Harmonic Resonance Theory – Does it Fit ?
The first theory is the possibility that the bending
modes of the barrel are getting excited differently each shot. Upon further
thought, I concluded that this is not possible, based on the following
reasoning. The basic resonant (beam bending or “ruler on the edge of the
desk”) mode of a cantilevered barrel (beam) made of steel at our typical
lengths and diameters is on the order of 500 to 1000 Hz, give or take. Even
if you look at higher order modes, such as the 5th harmonic mode,
you are still between 2500 to 5000 Hz. Keep in mind these modes are in
reality definitely NOT simple beam bending modes, but have a lot of twisting
and elongation going on at the same time as well, a very complex situation.
At 5000 Hz, the muzzle (assuming it was at a point of maximum movement)
would make one cycle every 1/5000 or 0.2 mS. If the dispersion was due to
these beam bending modes, then it should be fairly insensitive to small
changes in charge and seating depth. Also, changing the barrel mass
distribution even a little will completely change the node position, and
therefore make it impossible for a universal OCW load to exist. Therefore, I
concluded that the sensitivity to small changes was not from changes in the
bending modes.
A Theory to Fit #1
Having said this, I do agree that the POI changes are
primarily due to the bending modes, but because they are so low in
frequency, they are “smooth” and do not change rapidly over load variations.
I can explain this better using an RF engineering analogue. The barrel is
akin to a low pass filter, taking the mechanical input from the chamber
pressure profile, and “filtering” it through a complex resonant structure to
arrive at a muzzle position and bore exit angle time variation. The pressure
pulse is quite fast, reaching max pressure in around 0.4 mS typically, with
lots of little “bangs and clangs” going on as the firing pin strikes the
primer, the primer explodes, the pressure starts to rise and move the
bullet, the bolt slams back, and the bullet engages the rifling. All of this
happens in well under 0.1 mS (100 microseconds). The mass of the barrel
precludes this very fast excitation from getting to the muzzle in any
significant amount. It will start to “ring” but won’t get really shaking
until the bullet has left. This filtering makes the muzzle position very
insensitive to the charge and seating depth.
This model of a bending and vibrating barrel
explains the first observation above, and why an OCW load works, as it means
that the charge/bullet combination has a very consistent pressure profile,
and tends to excite the bending modes in a very regular way, keeping the POI
fairly constant.
However, since it ruled out the bending modes out as an
explanation for the variation in dispersion and velocity deviation, I was
still left with no model for these observations.
Epiphany
Two things came together for me at about the same time,
making a unified model possible. First, I read on one of the shooting forums
a post from a benchrest fellow about a barrel that he had that was his best
ever shooter. He had slugged the barrel, and found that the muzzle was just
ever so slightly smaller than the rest of the bore, on the order of one or
two ten-thousandths as I recall. His theory was that this was the best
possible case for a clean exit, as the bore constriction ensured no gas blow
by. Secondly, I remembered one visit to a very tall TV tower in central
Maine many years ago. I was killing time waiting for some event to happen (I
don’t remember what) and was playing with some truly immense guy wires
keeping the 1400-foot tower up in the clouds. These wires were about 3
inches in diameter, and were at least 1000 feet long, and under tremendous
tension. I remember grabbing the wire near the dead man anchor, and giving
it a shake as hard as possible. I watched the s-shaped wave disappear into
the overcast, only to appear a few seconds later, hit the anchor point, can
go back into the clouds, and so on until it died out. I played with this
like a 2 year old for quite a few minutes. Later on, as an RF engineer, I
built many circuits that used sections of transmission line to delay and
shape pulses, just like the pulse on the guy wire. Now, guy wires, RF
transmission lines, and rifle barrels are very different things, but physics
is physics, regardless of the field of use.
Traveling Wave Theory
Here is the second and crucial part of the model:
The pressure pulse from the gasses in the chamber
cause a traveling wave of stress that bounces back and forth along the
barrel between receiver and muzzle, slightly changing the bore diameter in
the process. Minimum dispersion of the shots will result when the rate of
change of the bore diameter is at a minimum, and this dispersion will
present the least sensitivity to load variations (charge, seating depth).
It is the position of this wave and its effect on the
muzzle at the point of bullet exit that is the cause of the majority of the
dispersion around the mean POI.
Stress Waves
Treat the barrel as a “conductor” of sound or applied
stress, and imagine for a moment that it is infinitely long. If you bang on
your section of the barrel with a hammer, it will generate an acoustic or
stress wave in the steel, which will travel in both directions away from the
hammer impact point at the speed of sound in the barrel. The stress wave is
a wave of force on the steel, some of which is in the radial (in and out
from the bore across the direction of travel) direction, called a transverse
stress component, and some of which is in the direction of travel, called a
longitudinal stress component. An acoustic wave in air is primarily
longitudinal, where the air compresses and expands along the direction of
travel. In a solid, such as steel, both components can exist at the same
time. In our infinite barrel, the wave travels on and on until the
mechanical losses in the steel dissipate the stress energy as heat.
Reflections
However, we do not shoot infinitely long barrels, so
what happens to the stress wave in a real rifle barrel? Just like in the TV
tower guy wire, if a stress wave reaches a mechanical discontinuity in the
object it is traveling in, such as the muzzle end of the barrel, or the
solidly bedded receiver end of the barrel, it will reflect back in the
opposite direction. In steel, the speed of sound is very close to 0.227
inches per microsecond, or about 18916 FPS. A wave will travel from the
receiver to the muzzle in the barrel in about 0.12 mS. It can make around 4
or 5 round trips before the bullet leaves. Note that it does not matter how
heavy the barrel is, or the profile, as the wave travels at almost exactly
the same speed in all cases.
Stress Causes Strain or Distortion of the Muzzle – Explaining
Observation #2
What does this stress wave do? Remember that stress is
the amount of force or pressure applied to a material, which usually results
in the material moving, bending, or displacing. This is called strain. So,
the pressure stress from the gasses in the chamber causes a resulting strain
in the barrel. Because the stress is applied very rapidly, the some of the
stress launches down the barrel as a wave, causing a proportional strain to
the barrel as it passes. This strain is initially a slight enlargement of
the bore, followed by a slight constriction, eventually dropping off to no
change in the bore diameter at all.
As this pulse travels to and fro, it passes by itself,
and in the process constructively and destructively adds to itself, all in
some predictable way. The shape of the pulse is driven by the pressure/time
profile from the propellant burn, and the mechanical properties of the
barrel. The theory nicely provides an explanation why very small changes in
load parameters could result in large changes in dispersion. If the muzzle
diameter is changing very rapidly at a particular time after shot
initiation, and if the bullet exits at this time, then very small changes in
the load will result in small changes in the exit time, but large changes in
the exit direction since the muzzle diameter is always different. Think of
this as a dynamic variation of the muzzle crown shape. It is well known that
the crown is perhaps the most critical part of the barrel as regards
accuracy. So, this theory or model can explain the sensitivity to the load,
and explain observation #2 above.
Model and Simulation
Nice theory, but where is the proof? To prove a theory,
you have to first make a model that can (hopefully) predict the behavior of
the real system, and then use that model to predict the outcome of some
controlled experiments. If the experimental data fits the model data, then
you can at least say that the test did not disprove the theory.
To test this theory, I constructed a model of a rifle
barrel using Matlab. Matlab is a very powerful engineering programming and
analysis tool, and is perfectly suited to this sort of analysis. I used a
simple filter model of the barrel to predict how the stress wave would look
when excited from a perfectly sharp hammer blow, or unit impulse. This is
shown in Figure 1 below.
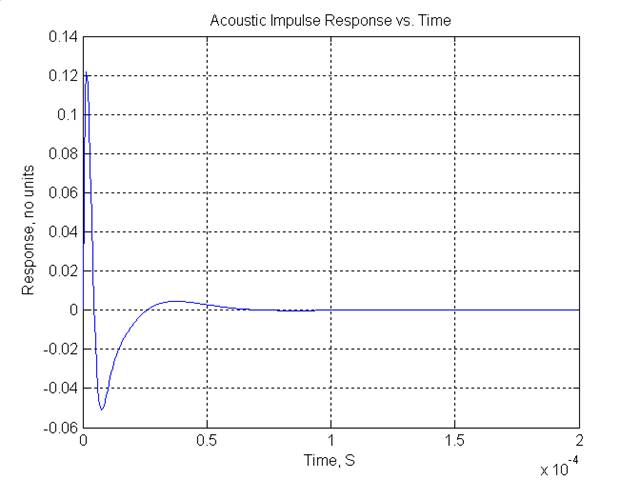
Figure 1 - Acoustic Impulse Response
The pressure versus time curve was taken directly from
a Quickload analysis of my accuracy load for my .223 Remington Ackley
Improved with a 27” barrel. This is 75 grain Hornady AMax over 25.5 grains
VVN140, at about 2950 FPS. The pressure curve is shown in Figure 2.
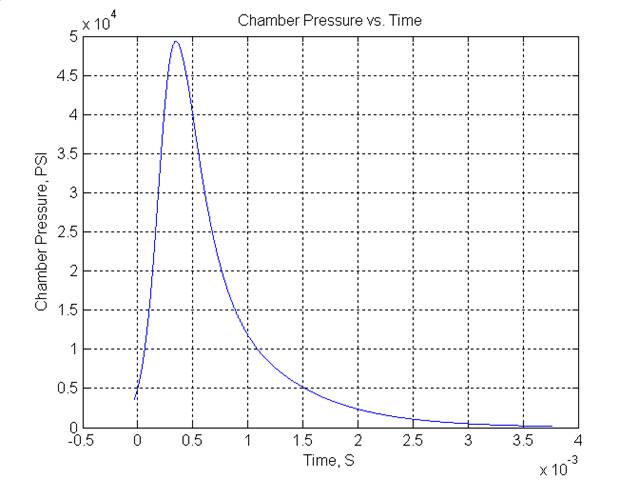
Figure 2 – Chamber Pressure versus Time
Now here the model gets a bit complicated. In reality,
the pressure does not stay in the chamber, but actually follows the bullet
as it travels down the bore. To make this first simulation computationally
tractable, I made the assumption that the pressure pulse was always
concentrated at the chamber end, and did not take into account the bullet
movement. Future versions of this simulation will include this effect.
However, this is more than good enough to get a first order look at the
system. So, if you take the pressure pulse and pass it through the filter
(barrel) that has the impulse response shown in Figure 1,
the resulting traveling stress wave looks like Figure 3.
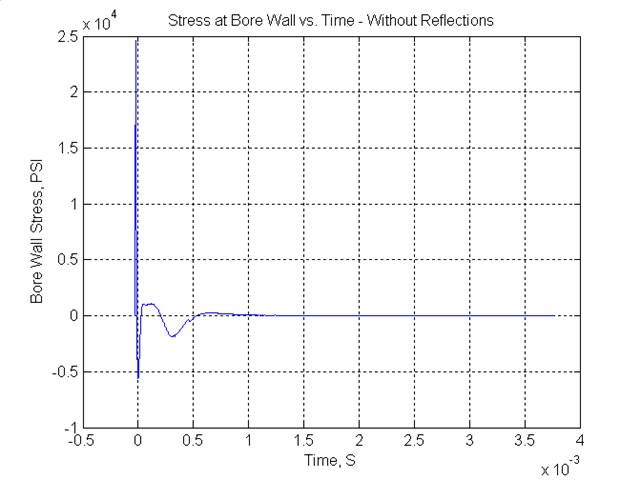
Figure 3 - Bore Stress versus Time
Figure 3 shows the
stress wave as if the barrel were infinitely long. Of course, this is not
the case, so we have to make the model simulate the effect of this wave
reflecting back and forth. Notice that the pulse has some interesting “tail”
responses about 0.5 mS after the main disturbance. These are due to the
differentiation of the main pressure peak by the barrel response, and turn
out to be the most significant feature of the whole system.
The simulation computes the addition of this pulse at
every point in the barrel, at every time point in the simulation. Matlab can
even animate the pulse as it travels to and fro. The barrel length, while
27” from bolt face to muzzle, is actually only as long as about the middle
of the chamber to the muzzle, from this pulse point of view. Until I get a
chance to electronically instrument a barrel, I will continue to use this as
my effective barrel length. This is just a guess and a convention, but is
subject to change until more data is accumulated. So far, this assumption is
holding up.
However, we are most interested in the stress at the
muzzle as time progresses. A plot of the muzzle strain (diameter change) as
a result of this stress is shown in Figure 4.
Again, please remember that this is a simple simulation of the muzzle
strain, and does not include the harmonic vibrations, recoil, or other
disturbances that occur in the real world.
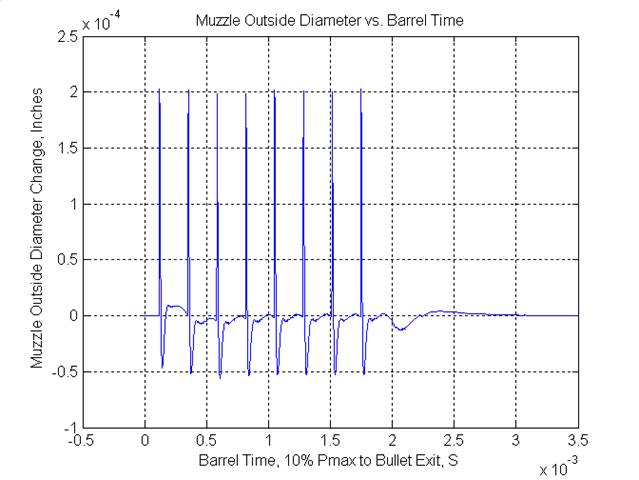
Figure 4 - Muzzle Bore Diameter Change versus
Time
Notice that the simulation carries on even after we
know the bullet has exited, in case at about 1.24 mS according to Quickload
Zooming in around our exit time, we can see that the
muzzle has some interesting behavior in this area of time, Figure 5.
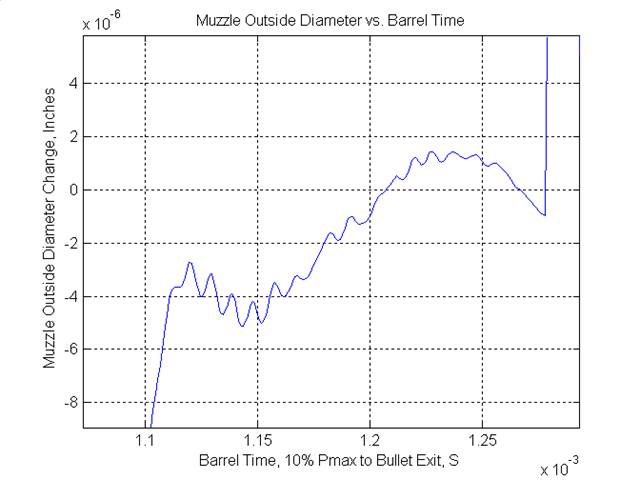
Figure 5 - Muzzle Disturbance at Bullet Exit Time
A Theory to Fit #2 and #4
The theory states that if the bullet leaves at the time
when the rate of change of the muzzle diameter is minimum, the dispersion
will be at a minimum, and any small variations in exit time caused by load
variations will have a minimum effect on the dispersion. Notice that the
bullet exits (1.24 mS) right when the rate of change in muzzle diameter is
at a minimum. Also notice that at around 1.05 and 1.28 mS, the pulse is
right at the muzzle, and the diameter is all over the map. In fact, the best
spot is (for this particular round trip cycle) at 1.24 mS, or just before
the pulse comes back again. There is another, not as wide in time, sweet
spot at about 1.15 mS.
Therefore, this theory and model seems to predict the
optimum exit times based on barrel length alone, where the group dispersion
is at a minimum. This supports observation #4 above.
Optimum Barrel Times
The simulation was used to predict the optimum bullet
barrel dwell times (10% Pmax to exit) as a function of barrel length, as
shown in Table 1:
Optimum Barrel times vs.
Barrel Length - Node Number as Parameter |
Barrel
Length, Inches |
node # |
16 |
17 |
18 |
19 |
20 |
21 |
22 |
23 |
24 |
25 |
26 |
27 |
28 |
29 |
30 |
1 |
0.550 |
0.580 |
0.610 |
0.645 |
0.670 |
0.700 |
0.790 |
0.810 |
0.825 |
0.855 |
0.883 |
0.915 |
0.940 |
0.970 |
1.000 |
2 |
0.590 |
0.640 |
0.680 |
0.720 |
0.760 |
0.775 |
0.840 |
0.870 |
0.900 |
0.945 |
0.978 |
1.005 |
1.035 |
1.060 |
1.090 |
3 |
0.685 |
0.725 |
0.765 |
0.805 |
0.840 |
0.880 |
0.980 |
1.005 |
1.030 |
1.070 |
1.110 |
1.150 |
1.185 |
1.220 |
1.260 |
4 |
0.725 |
0.785 |
0.835 |
0.880 |
0.930 |
0.955 |
1.030 |
1.065 |
1.120 |
1.160 |
1.200 |
1.240 |
1.275 |
1.310 |
1.345 |
5 |
|
|
|
|
|
|
|
|
|
|
1.330 |
|
1.425 |
1.470 |
1.520 |
6 |
|
|
|
|
|
|
|
|
|
|
|
|
|
1.560 |
1.605 |
Table 1 - Predicted Optimum Barrel Times
These times were obtained by running the
simulation at each barrel length, the visually determining the time
of least muzzle diameter change for each round trip.
One of the major observations was that OCW
loads tend to work well in almost any rifle, regardless of barrel
length. This observation forced us to abandon the concept of a
simple harmonic vibration as being the cause of dispersion. So, how
does a given load (bullet, case, powder, and specific charge weight)
work if we use that same load in rifles with different barrel
lengths?
The accuracy load developed for the .223 AI 27”
rifle was used as the constant in Quickload, and the barrel time was
computed in Quickload after changing only the barrel length. This
was plotted against the model simulation of the muzzle disturbance
over the same length of barrels, with the best exit time chosen for
each length, for the same round trip number. Figure 6
shows this data. The blue line with diamond markers shows the
relationship, with each marker corresponding to a particular barrel
length. The 16” length point is the marker to the far left, and the
27” length point is at the far right. It is nearly a straight line,
as expected. However, it does not track exactly one for one with
barrel length, and shows some divergence as the length is shortened.
The purple line is what an exact one for one relationship would be.
It is interesting to note that the relationship is very close to one
to one from about 24” to 27”, the length range that in which the
vast majority of bolt action rifles are produced. This shows that
the ability of an OCW load to work well across many rifles is
supported by this theory and model.
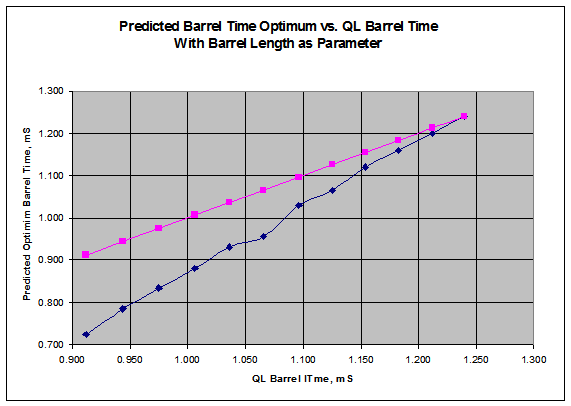
Figure 6 – Quickload Predicted Barrel
Time for Given Load as Compared to Predicted Optimum Barrel Time
A Theory to Fit #3
So, we now have a model that supports
observations #1, #2, and #4. What about observation #3? Can it
explain the extreme sensitivity to seating depth of the group size
and the rapid changes in velocity deviation?
Bullet Modulation
I believe the theory does explain this
sensitivity, for the following reason. Since the pulse is changing
the bore diameter as it passes back and forth, it seems reasonable
that the bullet frictional load is also changing as the bore
diameter changes. During the first two or three trips back to the
chamber end, the bullet has moved by less than two inches, and the
pressure is at or near maximum, Figure 7.
If the bore constricts, it will cause the bullet to be retarded
some, and thereby increase the pressure rate of increase.
Conversely, as the bore expands after the first part of the pulse
passes, the bullet will be looser, and the pressure increase rate
will drop. In other words, the pulse, by interacting with the bullet
during the critical first few inches, can dramatically change the
burn characteristics by modulating the bullet retardation forces.
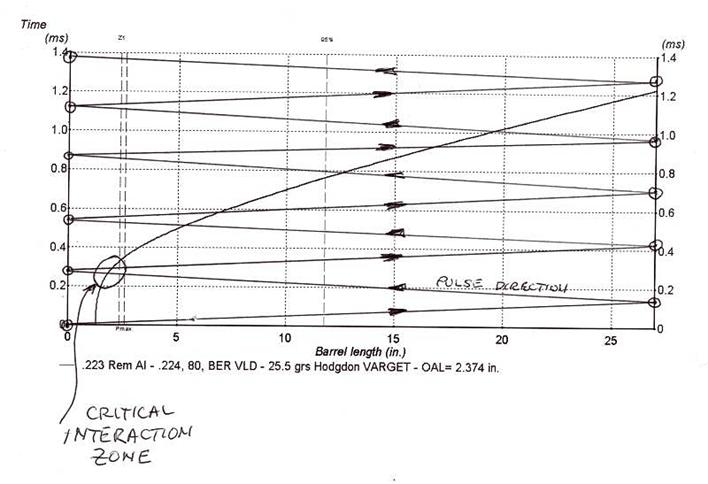
Figure 7 - Pulse Reflection Superimposed
over Bullet Position versus Time
To understand this, we need to look at how
propellants burn in a cartridge. Propellant burn rates are
controlled by many factors, but in general they burn faster at
higher pressures and slower at lower pressures, especially in the
initial stages of combustion. During the initial stage, the powder
is not all lit, and the flame front is moving out to all the grains.
In the intermediate stages, all the grains are lit, and gas is being
produced at a rate that is a function of the pressure and
temperature and the powder characteristics. In the final stages, the
gas production rate is dropping off as the grains become consumed.
Any systematic effect that varies the chamber
pressure or volume during the initial stages can dramatically change
the pressure peak time. If a load is not very heavy and the case is
not very full, the initial stages last longer than in a load that is
near max. All the OCW loads developed with this theory have been
found to work best when the powder charge is near max volume for the
case and bullet combination. This also explains why variations in
neck tension and seating depth can have an (sometimes) adverse
affect on accuracy and velocity variations. Granted, this is not at
all new, but now there is a consistent explanation for why this is
so.
The modulation in pressure by the interaction
of the reflected pulses and the bullet will slightly change the
position of the bullet on the next pulse pass, further changing the
burn. The nest result is that the overall burn becomes chaotic,
which by definition is any process that exhibits extreme sensitivity
to initial conditions. On the other hand, if the timing of the pulse
over the bullet is after the powder reaches the intermediate point,
then the modulation effects become less significant.
So, the reason why we see very significant
group size changes by changing the seating depth (question #2 above)
can now be explained by the interaction of the pulse with the bullet
during the initial stages of propellant combustion. The rate of
burn, and hence the actual barrel time will be varied a lot by small
changes in the amount of time it takes for the pulse to comeback
over the bullet. Question #3 is also explained simultaneously as #2,
since they are really one in the same, as changes in barrel time
result in changes in muzzle velocity. We need only to be sure that
we choose a powder and charge volume that insures that the powder is
out of the initial stages before the first return trip of the pulse.
Comparing Model Predictions and Real World Range Results
So, how does this model hold up to the real
world? In a word (well, two words), almost perfectly. I say almost,
since there is enough error in Quickload and in the ability to
estimate the precise effective barrel length that the actual power
charge needed for optimum groups was usually about 1 to 2 percent
less than Quickload predictions. Note that Quickload uses the time
from 10% of maximum pressure the bullet exit as the definition of
barrel time. I have adopted this as my definition in order to keep
my use of Quickload as simple as possible.
Even given these potential sources for modeling
error, I was able to validate that the optimum barrel time for this
223AI rifle with its 27” barrel is right at 1.24 mS, for multiple
powders. Since I could not get the 75 grain bullets to exit in 1.15
mS without greatly exceeding the maximum pressure, I tried using 55
grain Vmax bullets, and again had minimum groups sizes at exactly
the expected barrel time of 1.15 and 1.05 mS. I noticed that the
load sensitivity here was higher than at the slower load, which is
predicted by the narrower stable time period at 1.15 mS. See Table 2
and Table 3. These tables document
the loads used to validate the model with 75 and 80 grain bullets,
my primary desired projectiles for this project rifle. They show the
measured group sizes, velocity performance, and the predicted data
from Quickload. All loads were shown to provide the best groups and
minimum POI shift, over the widest variation in charge weight and
seating depth. They are true OCW loads.
Rifle: |
Savage 12FV with PacNor SSSM 1:8 27" barrel, Leupold 8.5-25X50 LRT,
glass bedded Bell & Carlson Stock |
Caliber: |
.223 Remington Ackley Improved |
Load Data: |
Updated 8/31/03 |
|
|
|
|
|
|
|
|
|
Measured |
|
|
|
|
|
Bullet Manufacturer |
Bullet Style |
Bullet Weight, gr |
Powder |
Charge Weight, gr |
COL to Datum, in |
COL to Tip, in |
Primer |
Brass (Fire-formed) |
Average Muzzle Velocity, FPS |
Extreme Velocity Spread, FPS |
Velocity Standard Deviation, FPS |
100 Yard 5 Shot Group Size, in |
200 Yard 5 Shot Group Size, in |
QuickLoad Velocity, FPS |
QuickLoad Barrel Time, mS |
Notes |
Hornady |
Amax |
75 |
Win 748 |
25.0 |
1.892 |
2.397 |
CCI BR-4 |
LC |
2857 |
14 |
7 |
- |
0.700 |
2951 |
1.249 |
|
Hornady |
Amax |
75 |
IMR4895 |
24.5 |
1.892 |
2.397 |
CCI BR-4 |
LC |
2911 |
40 |
20 |
- |
0.550 |
2945 |
1.240 |
|
Hornady |
Amax |
75 |
Varget |
24.4 |
1.892 |
2.397 |
CCI BR-4 |
LC |
2882 |
43 |
17 |
- |
0.650 |
2884 |
1.259 |
|
Hornady |
Amax |
75 |
VVN140 |
24.3 |
1.892 |
2.397 |
CCI BR-4 |
LC |
2887 |
13 |
4 |
- |
0.600 |
2858 |
1.277 |
|
Berger |
VLD |
80 |
Varget |
25.5 |
1.850 |
2.374 |
CCI BR-4 |
LC |
2952 |
33 |
12 |
0.600 |
- |
2968 |
1.188 |
Too fast |
Berger |
VLD |
80 |
Win 748 |
25.0 |
1.850 |
2.374 |
CCI BR-4 |
LC |
2880 |
47 |
21 |
- |
0.700 |
2923 |
1.244 |
|
Table 2 - .223 Remington Ackley Improved Optimum Load Data - Original
Throat
Rifle: |
Savage 12FV with PacNor SSSM 1:8 27" barrel, Leupold 8.5-25X50 LRT,
glass bedded Bell & Carlson Stock |
Caliber: |
.223 Remington Ackley Improved |
Load Data: |
Updated
10/18/03 - throat moved out 0.100 |
|
|
|
|
|
|
|
|
|
Measured |
|
|
|
|
|
Bullet Manufacturer |
Bullet Style |
Bullet Weight, gr |
Powder |
Charge Weight, gr |
COL to Datum, in |
COL to Tip, in |
Primer |
Brass (Fire-formed) |
Average Muzzle Velocity, FPS |
Extreme Velocity Spread, FPS |
Velocity Standard Deviation, FPS |
100 Yard 5 Shot Group Size, in |
200 Yard 5 Shot Group Size, in |
QuickLoad Velocity, FPS |
QuickLoad Barrel Time, mS |
Notes |
Hornady |
Amax |
75 |
IMR4895 |
25.5 |
2.020 |
2.525 |
CCI BR-4 |
LC |
2913 |
60 |
21 |
0.300 |
- |
2989 |
1.226 |
25.3? |
Hornady |
Amax |
75 |
IMR3031 |
24.5 |
2.020 |
2.525 |
CCI BR-4 |
LC |
2998 |
34 |
13 |
- |
0.576 |
2993 |
1.238 |
|
Hornady |
Amax |
75 |
VVN140 |
25.5 |
2.020 |
2.525 |
CCI BR-4 |
LC |
2938 |
51 |
12 |
0.280 |
0.476 |
2917 |
1.250 |
|
Table 3 - .223 Remington Ackley Improved Optimum
Load Data - Extended Throat by 0.100”
With this model, I was able to arrive at the
optimum charge weight almost without any workup, as I could start just
below the weight predicted, and observe the groups as the charge was
slowly increased. I usually started with the bullets right on the lands.
Interestingly, I could often take an optimum load with the bullet on the
lands, and by seating the bullet deeper and deeper, pass thought a
region of poor groups, until the group would tighten back up again. This
ended up being another optimum, especially if I slightly reduced the
powder charge enough to get the pressure/velocity back down to about the
same as the on the lands case.
I shot hundreds of combinations, and looked at each
and every load worked up in the past with respect to the predicted
barrel exit time and the optimum. In all cases, with no exceptions was
the best load off the predicted exit time by more than 2%. In addition,
they exhibited all the characteristics of an OCW load, being insensitive
to charge weight, and small changes in seating depth (+-0.010”). I have
asked others to validate this model, and am awaiting their results.
Summary and Conclusions
So, we now have a theory and a model that can
predict the optimum barrel times given only the barrel length,
regardless of barrel construction or mounting. Given this barrel time,
we can use an internal ballistics program such as Quickload to find
powder and charge weight combinations that fulfill the simultaneous
requirements of:
- Filling the case as full as
possible, thereby ensuring the most rapid initial stage possible
- Ensure that the powder is
all lit before the first pulse passes back over the bullet at the
chamber
- Meet the overall barrel
time requirement based on the length of the barrel
Next Steps
I am planning to instrument a barrel with both
strain gauges and acoustic sensors (microphones) in order to get hard
confirmation of the above theories. I will update this document as that
information becomes available. Any comments, questions, or suggestions
can be directed to me at
My Email Address
.
Good shooting!
UPDATE 8/8/04
Thanks to Dan (green788), David (LTRDavid), and
countless others, it appears that this theory is proving to be quite
accurate in predicting the barrel times for the smallest groups. These
data have been accumulated over a large number of rifles, calibers,
loads, and conditions. The process of using QuickLoad to find a good
choice of powder and charge weight for a given barrel length seems to be
very effective, especially if the powder burn rate and cartridge
weighing facto is calibrated to the actual rifle based on measured
velocity and pressure data. The author has used the PressureTrace
instrument along with an Oehler chronograph to great effect when loading
at the range. With QuickLoad running on a laptop, instant estimates
regarding the load can be made, and appropriate changes can be made to
very quickly find the OBT/OCW load for the particular powder/bullet
being tested.
We cannot stress enough the value of using
PressureTrace during this process. It allows you to not only see how
QuickLoad matches the velocity, but how the chamber pressures match as
well. You can quickly eliminate powder/primer/case/seating depth
combinations before wasting a lot of effort on them, as the pressure
curves will show the variations in velocity as well as the chronograph,
and together you get a very clear picture of how the system is working.
In addition, since it provides a quantitative measurement of pressure,
you always know when you are pushing the envelope in terms of the load
level, and can measure the effects of temperature changes as well. The
author takes an electric heating pad to the range, and hot soaks 10
rounds in the pad to get them to about 125F. Fire them before they have
a chance to cool off, and you can see immediately how the load will
handle extreme temperatures in the field.
We have distilled the visual OBT observations into
a (fairly) simple equation to be used to compute the OBT for a barrel of
any given length. Simply substitute the numbers A through C into the
equation, choosing the set from the left column if the node number N is
odd, and the right column if the node number is even. The node number is
arbitrary, and can be zero or negative.
|
MASTER MODEL |
|
|
|
|
|
N Odd |
N Even |
|
|
|
A |
4.42642857E-03 |
4.40803571E-03 |
B |
2.84942857E-02 |
2.68380952E-02 |
C |
-3.18785714E-03 |
-2.40148810E-03 |
D |
2.91180952E-02 |
4.39015873E-02 |
|
|
|
|
OBT = (A*N + B)*L + C*N + D
|
|
|
|
|
N is node
number, may be zero or negative |
|
|
L is barrel
length in inches |
|
OBT is in mS |
|
As an example, if the barrel is 24 inches long, and
you desire to find the OBT for node 4, the equation would look like:
OBT = (4.40803571E-03
* 4 + 2.68380952E-02)*24.0 + (-2.40148810E-03 * 4) + 4.39015873E-02 =
1.101 …
You will find that the above equations will give
OBTs slightly different from the table values in the above text. This is
due to the effects of the inevitable human error in visually estimating
the OBTs, and the fact that the equation is a distillation of the
original data, and does not match the data perfectly). These variations
can be ignored, as the variations in powder lot burn rates are more
extreme than these model errors.
If you try this approach, please send me your
observations if you have the time.
Acknowledgements
I would like to than Dan Newberry for all his help
in this investigation. Without his prodding, I would never have embarked
on this journey. I would also like to thank my wife and family for all
the free Saturdays at the range, giving me the time to try all the load
variations. Without their patience this would not have been validated.
Any use or reproduction of this material for sale
or profit without express permission of the author is prohibited.
Copyright 2003-2004 by Christopher Long
Use this material at your own risk
|
|